Precision Steam Control
Jordan Sliding Gate Valve for Precise, Efficient Steam Control
The Jordan sliding gate valve technology is designed to deliver more efficient control than traditional valves. Using Jordan sliding gate steam valves in industrial steam applications reduces cost of ownership with more efficient steam control and less maintenance cost.
How does the sliding gate valve work?
The sliding gate seat is made up of a movable disc and stationary plate each with matching multiple openings. When the valve is fully closed, the disc and plate are aligned such that the openings are covered, creating a tight Class IV shutoff. As the valve opens, the slots are gradually uncovered and fluid flows straight through until the desired set point is reached. The disc modulates its position to allow process fluid to flow and maintain the set point.
This sliding gate seat set achieves levels of performance, reliability and accuracy that are hard to find in other designs.
Why the Sliding Gate Valve Outperforms in Steam Service
The Jordan sliding gate valve is designed for industrial use where long term operation and lower overall cost of ownership are important.
Jordan sliding gate valve lasts longer
In a sliding gate design, the product travels straight through the valve, minimizing turbulence and wear. Conversely, in a Globe style the product flow changes direction three times leading to higher velocity and flow turbulence, causing more wear on the seat components.
Jordan Valve sliding gate seats, with their advanced Jorcote coating, have demonstrated minimal wear for over one million cycles in high-pressure steam service. When the sliding gate opens, steam travels straight through multiple openings, distributing the erosive exposure of steam across surfaces and minimizing wire draw often occurring in traditional steam valve designs.
- Longer valve seat life results in less maintenance and downtime.
Sliding gate delivers more accurate control
The control element in the Jordan sliding gate valve is perpendicular to the process flow and has a short stroke length. Combined with the multiple openings, this seat design allows faster more accurate control and minimal droop. The process flow path is into the disk, minimizing valve chatter and improving stability at the low end of stroke. Because it responds quickly to input signals, Jordan sliding gate valve reaches pressure and temperature setpoint quicker.
- More accurate control and faster response results in steam savings.
Sliding gate valve operates with less energy
The stroke length of the sliding gate valve is a fraction of an inch. This not only results in faster reaction times, but the short operating path requires less force to operate. It also significantly reduces the stresses on the packing and the valve actuator.
- Savings adds up with reduced energy consumption.
Jordan valve overlapping design creates tight shut-off
The disc and plate are designed with a slight overlap of the openings to provide an ANSI Class IV shut-off rating. Each orifice is engineered with a 1/32” overlap creating an area of closure versus a line of closure as seen in globe valves.
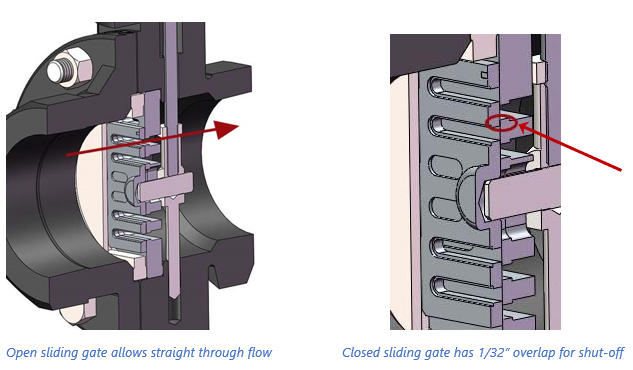
This seat overlap in the Jordan Sliding Gate Valve is an important advantage. If there were any damage to the leading edge of the valve seat due to steam erosion, it would be covered when the sliding gate closes, ensuring full shut-off.
- Area of closure design has better long term shut-off.
Sliding gate design generates less noise
Compared to conventional globe and cage designs, the sliding gate seat generates between 5-10dB less noise. The sliding gate valve is quieter than other traditional valves for several reasons: The disc and plate remain in constant contact, eliminating the chatter; The straight-through flow passage minimizes turbulence, a significant cause of valve noise; And the multiple orifices in the plate and disc divide the flow into smaller flow streams, resulting in less noise.
- Save on premium costs of a “low-noise trim” by using the quiet sliding gate valve.
Let us help you find the right valve for your application.
Related Resources
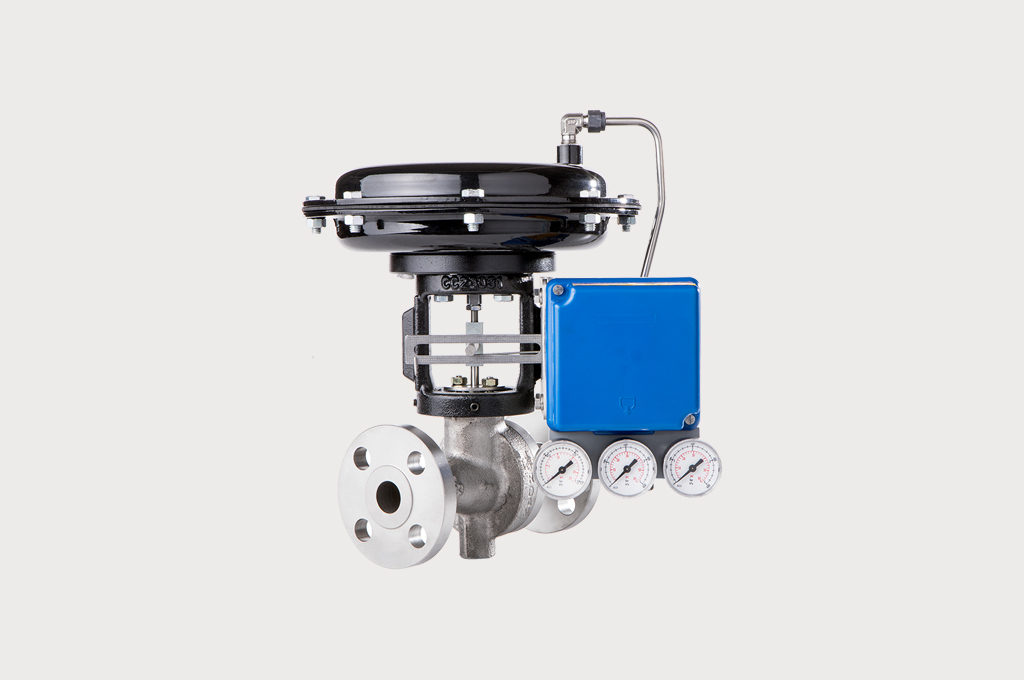
Steam Valve for Tire Curing Press
Jordan Valve sliding gate technology outperforms in challenging tire curing process
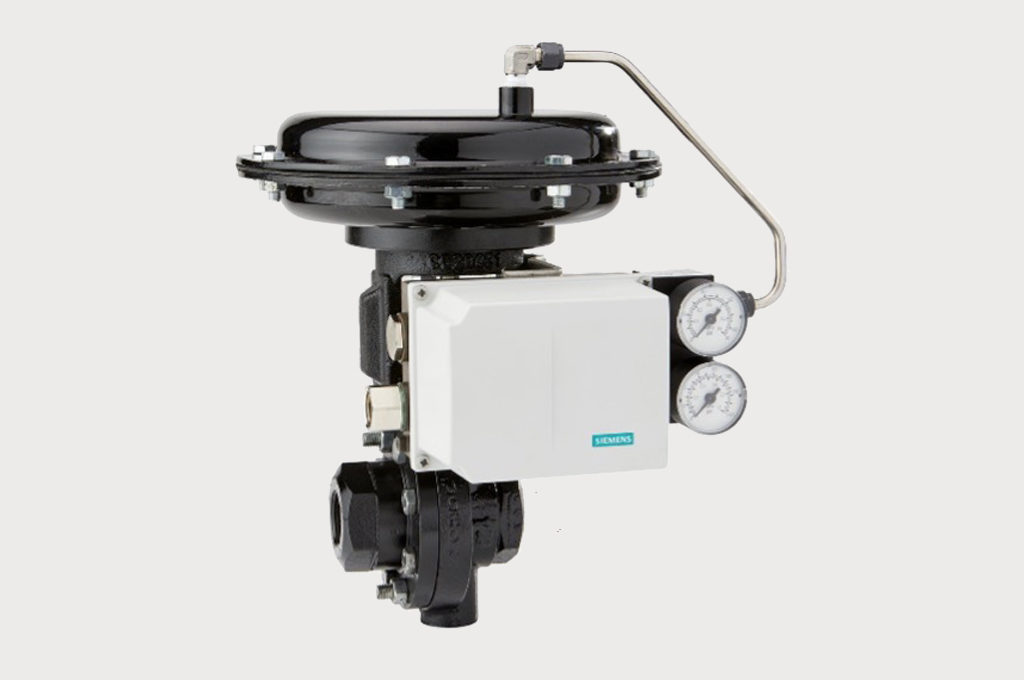
Better Steam Pressure Control Improves Drying for Coating Process
Jordan Mark 701 Sliding Gate Control Valves give Tighter Temperature Control, Faster Throughput
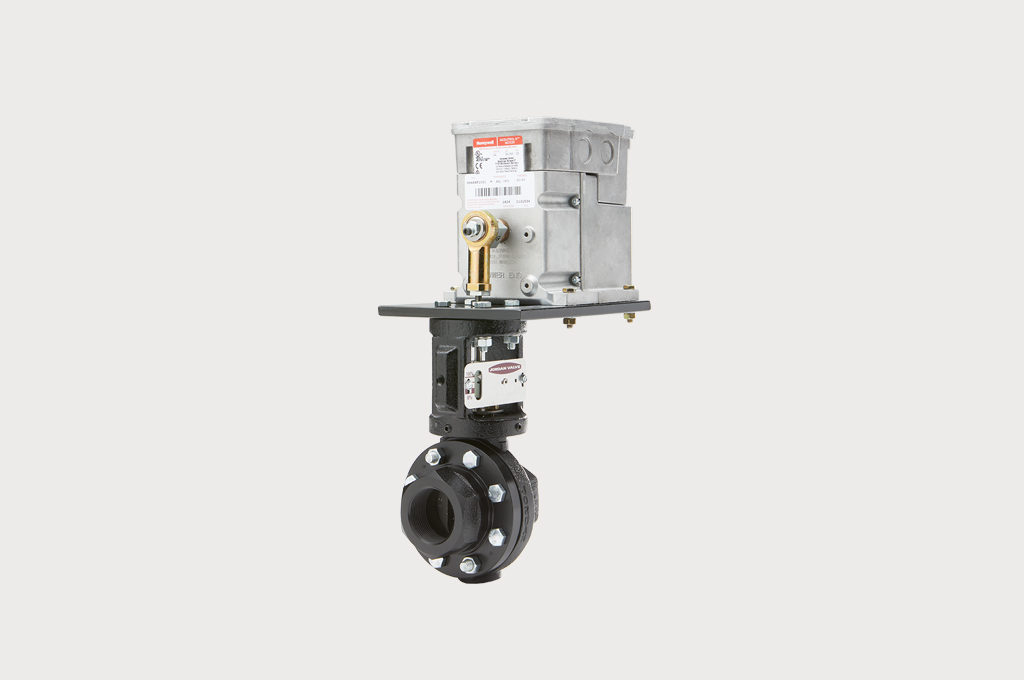
Boiler Feedwater Control
Jordan Mark 33 feedwater control valve maintains accurate level in boiler steam drum.
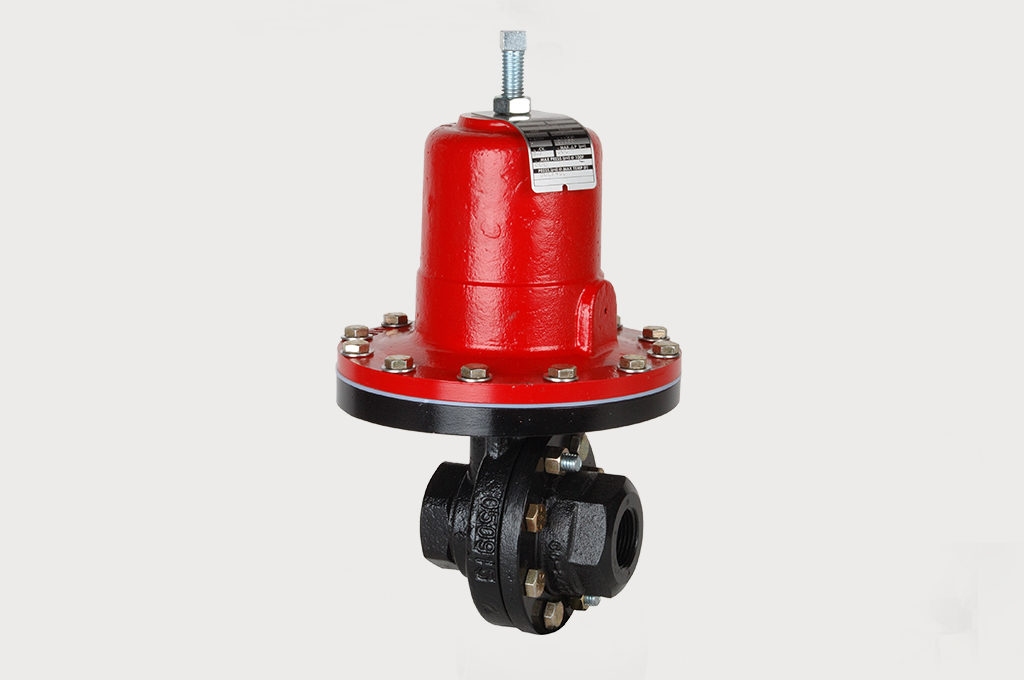
Steam Sterilization
Jordan Valve sliding gate valves with Jorlon® diaphragms outlast in challenging steam sterilizing process
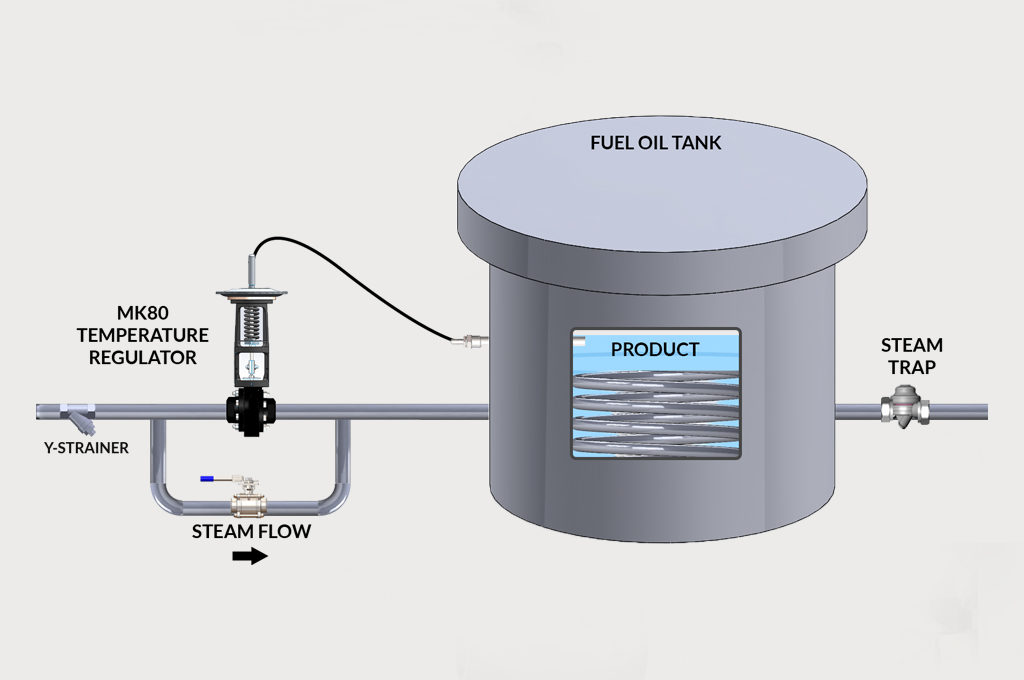
How Temperature Regulators and Control Valves Work
Using Self-Operated Temperature Regulators to Control Steam
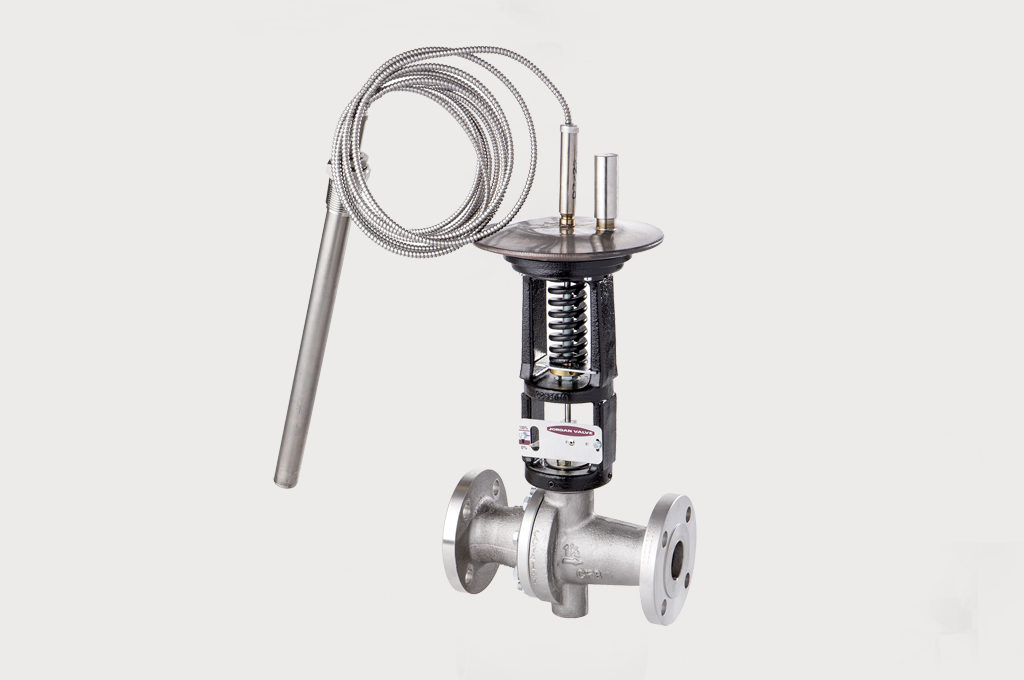
Steam Temperature Control of Jacketed Tanks
Steam pressure control is vital for maintaining consistent tank jacket temperature
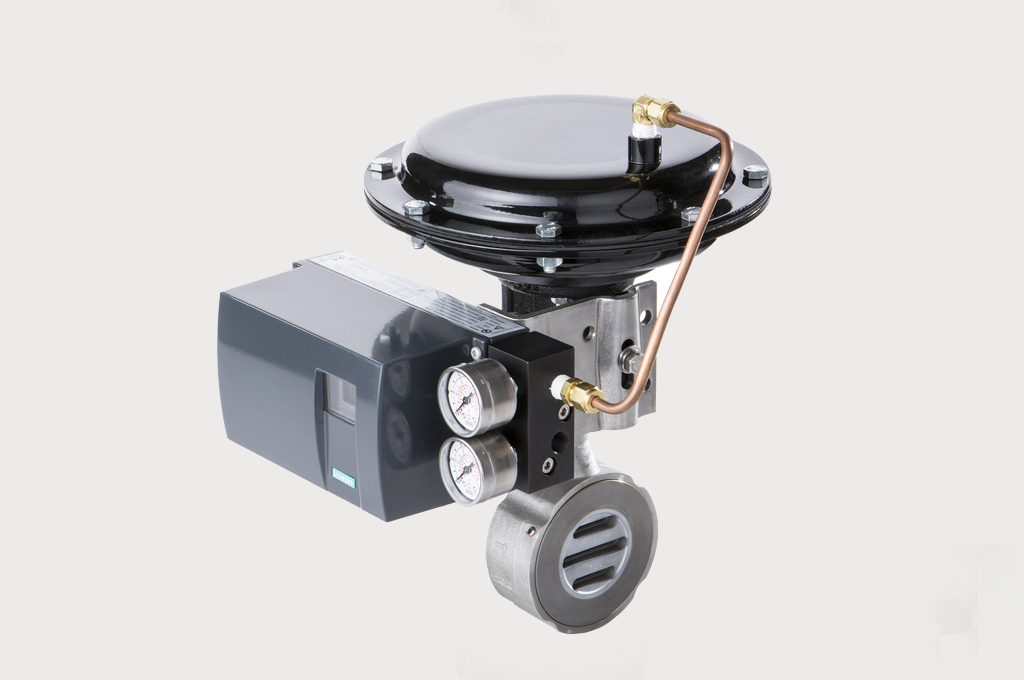
Steam Curing Cinder Blocks
Accurate steam control for precision autoclave dryer performance
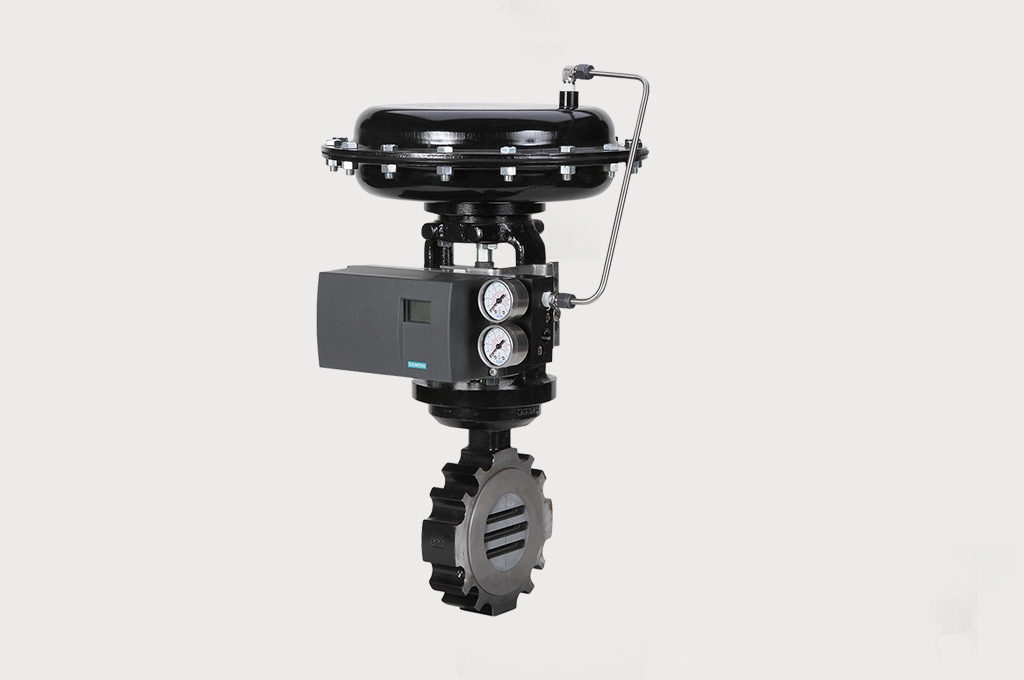
Precision Steam Control
Jordan Sliding Gate Valve for Precise, Efficient Steam Control